Getting EVs On Track With Simulation-Driven Virtualisation
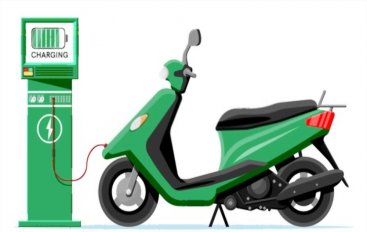
Transportation drives the global economy. It’s at the heart of both business and pleasure. With the world's population nearing 8 billion, all that travel definitely adds up. And what’s more? It’s taking a toll on the planet. Going forward, we need to find mobility solutions with a lower environmental impact. Electric vehicles (EVs) are today gaining more attention due to the increasingly strict government regulations in most countries, coupled with growing consumer awareness. All these are creating an unprecedented demand for efficient, environmentally friendly transportation.
EV Battery Safety
In the last couple of years, the EV industry has seen multiple setbacks. The first one was due to the Covid-19 pandemic and then due to the more recent EV fire incidents that were gaining attention all over. At the end of the pandemic, there were high expectations that were set for the EV market growth due to its role as the preferred personal transport means, but the multiple fire incidents started making headlines and it affected consumer confidence as well as brand value.
The battery is a key component of the vehicle. While EV makers race to be the first to come to the market with an extended range and high-speed charging, design engineers are under tremendous pressure to innovate such technology without compromising on the safety aspect.
Most of the fire incidents were related to poor cell quality, manufacturing defects, structural damage, poor charging system and BMS failure. The EVs, being relatively new, there is a lack of real-world data for battery performance. This means that OEMs need to accelerate their development and testing to be in the race to the market. The most cost-effective way to address the above challenges within the stringent delivery timeline is by adopting virtualization in every aspect of the battery pack development process.
Addressing EV Safety Concerns through Simulation Driven Virtualisation
We can divide the safety aspect of EVs into multiple categories like manufacturing defects, thermal, mechanical, electrical, and Battey Management System (BMS). Simulation-driven virtualisation practices can help battery development all the way from manufacturing to operational maintenance and safety. Battery manufacturing involves multiple processes like mixing, coating, drying, filling and more. Through virtualisation, a cell manufacturer can get more insights into the operational process and fine-tune the operating conditions to get homogenous mixing of active materials, binders and electrolyte. And in a coating process, the manufacturer can vary the flowrate to get uniform thickness on collector. Similar finetune operating condition can be done in the drying and filling operation to avoid any manufacturing defects and also improve the battery quality.
Temperature can significantly impact the performance of the Lithium-ion cell. The ideal operating temperature range for a Li-ion cell is 20⁰C - 40⁰C. Most of the battery cells are imported in India. They need to be tested in the Indian environment. Using simulation practices, a designer can validate battery performance under varying ambient conditions, drive cycles, load conditions, cooling techniques, and more. With simulation solutions, engineers can eliminate the expensive and time-consuming trial and error testing process as it uses a physical prototype.
As Lithium-ion batteries are high energy and power density cells, under thermal or mechanical abuse, a thermal runaway can occur resulting in an uncontrollable increase in temperature that can lead to fire and explosion. In such a scenario, the passenger needs at least 5 minutes of advance warning to be able to escape from the vehicle. As thermal runaways are instantaneous, there is a need for reliable hardware and software to mitigate the runaway.
The new hardware design consists of heatsink or phase change material around the cells to take away the heat and avoid runaway. By using simulation, designers can try different heat sink designs or materials to select the right combination to mitigate the runaway. When it comes to mechanical abuse, there are multiple tests which are performed for battery safety and reliability. Tests like the Nail penetration test (SAE J2464) for internal short circuit, Random vibration (SAE J2380) Drop Test (SAE J2464), self-weight (SAE J2380), and sore are some of them. These tests can also be performed virtually and we can get better insight into design, identify regions of high stress, modify the structural design to mitigate runaway and have a robust design.
One of the other reasons for thermal runaway is BMS failure. BMS is a control unit in the EV to sense, measure, and report crucial operating conditions for safe battery operation while protecting the battery from damage. The BMS includes embedded software for real-time monitoring and control of elements such as voltage, current, temperature, charge between cells and protects from overvoltage and ensures safe operation despite repetitive charging and discharge conditions. Traditionally, these BMS codes are burnt on hardware (HiL) for verification and validation. However, with simulation, designers can now bring the high-fidelity battery model plant and BMS on a single platform and integrate both to understand how the entire system (battery pack with BMS) performs. All this can be done virtually! Simulation has proven to increase the productivity in BMS development by 30 per cent for an automotive service provider while helping an OEM reduce the EV design cycle by 50 per cent.
To conclude, the EV battery incidences that we see today are temporary and short-lived. They will not derail the momentum that the industry has gained over the past 12 months. For an OEM, however, to keep up their promise of reliable and safe EVs, simulation-driven virtualisation will act as a catalyst to accelerate new vehicle development without compromising on safety.