Bosch Limited Inaugurates Bidadi plant
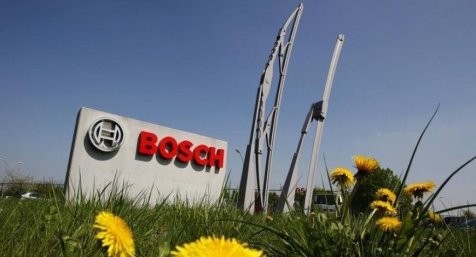
Bosch has inaugurated its expanded factory for mobility solutions in Bidadi (Phase II), which is located some 35 kilometers from Bengaluru. The plant features the latest Industry 4.0 solutions and carbon-neutral technology. “Bosch is taking a further step toward more efficient, more flexible, and sustainable manufacturing in India in order to boost competitiveness and meet rising demand in the local market,” said Volkmar Denner, chairman of the board of management of Robert Bosch GmbH. “The new Bidadi plant will further boost India’s strong role in the Bosch Group’s global network.” The company has invested 31 million euros in the new facility. The Bidadi plant will accommodate almost 2,500 associates by the end of 2019.
The Bidadi plant will act as a local hub for the development of Bosch powertrain solutions and manufacture of automotive products such as common rail single-cylinder pumps and high-pressure rails. “It is important for Bosch to leverage our expertise in manufacturing operations and combine it with technology and digitalization to build lean manufacturing facilities,” said Soumitra Bhattacharya, the managing director and president of the Bosch Group in India.
From Adugodi to Bidadi
Bidadi Phase I witnessed a shift of around 500 people from the existing manufacturing facility in Adugodi to Bidadi, along with manufacturing operations for the new-generation powertrain solutions products. Now, Phase II has witnessed the shift of around 2,000 people, as well as 760 units of machinery and equipment. This movement is one of the largest relocation projects ever undertaken by Bosch. The former Adugodi manufacturing site is being converted into a high-tech engineering center and is slated to become the largest Bosch technology campus outside Germany.
Sustainable manufacturing
Bosch plans to be fully climate-neutral as early as next year. It's over 400 locations worldwide, together with their engineering, manufacturing, and administrative facilities will no longer leave a carbon footprint. This will make Bosch the first major industrial enterprise to achieve this ambitious goal in a little over a year. In line with this target, the Bidadi plant has been built to be leaner and more sustainable. According to the International Energy Agency, manufacturing accounts for around 32 percent of global carbon dioxide emissions. To quote Dr. Volkmar Denner: “The current state of the global ecosystem demands that organizations make concerted efforts to reduce their global carbon footprint. We at Bosch see climate action as our responsibility and believe we have to act now. The company has undertaken initiatives to build environmentally friendly manufacturing sites across the globe, and the Bidadi plant is the latest result of this effort.”
The new facility is aligned with the blueprint of the “Carbon neutral – 2020” strategy, with initiatives such as energy analytics, environmental initiatives such as tree planting, the use of alternative fuel like Compressed Natural Gas for heating, and solar power capacity of 8.7 megawatts peak in 2018. The sun accounts for approximately 30 percent of the power consumed by the plant. The facility is built to be environmentally friendly and is a landmark in manufacturing practices across India.
Increased production efficiency
Bosch is a leading user and provider of Industry 4.0 solutions and is using them in Bidadi to increase the plant’s efficiency and competitiveness. In its manufacturing operations, the plant uses cobots (collaborative robots), automated visual inspection stations, and Device Bridge software, a local Bosch innovation that can be retrofitted to old machinery to turn them into connected devices, thereby significantly improving processes and reducing defects.
The Bidadi plant has put an intensive system continuous improvement process (SCIP) into place which is the way to achieve sustainable waste-free processes. This will allow it to further improve and maintain safety and quality standards while remaining cost-competitive. Modernizing the machinery and using smart automation solutions have helped make the plant more efficient, and already resulted in remarkable achievements.