Marelli Powers New Maserati GranTurismo Folgore With 3 High-performance E-motors
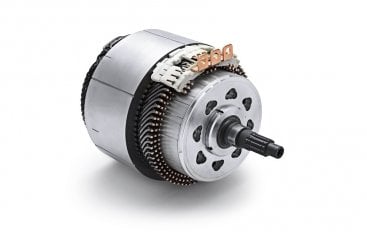
Marelli has the honour to contribute key technologies to this unique coupe, boosting in particular the superb performance of the Folgore version with the three e-motors equipping the first full-electric Maserati car. The extreme performance of the vehicle – with a total installed power of 1200 HP – are ensured by one of the most compact e-motor solutions on the automotive market, fully developed and produced in-house by Marelli at its Modugno plant (Bari, Italy). Both the product and the related specific and extremely efficient manufacturing process have been developed in a two-year span, a record time to market.
Marelli has also contributed to the exclusive lighting signature of the new Maserati Gran Turismo with full LED headlamps, that on specific trims also feature Adaptive Driving Beam Matrix system. In addition, on the connectivity side, the vehicle is equipped with Marelli’s Telematic Control Unit.
The e-Powertrain system of the Maserati GranTurismo Folgore is based on state-of-the-art 800V Marelli’s electric motors, one placed in the front and two in the rear e-axle, resulting from the company’s extensive know-how in motorsport electrification and flow-down to series production applications. Thanks to the high levels of power density reached (9.2 kW/kg) and the total torque of 1350 Nm, they ensure superb performance as well as driving comfort, with one of the best weight/power ratios on the market.
“We are really proud to provide our technologies for a vehicle that is marking such a memorable moment in the history of an iconic brand as Maserati” said Hannes Prenn, President of Marelli’s Electric Powertrain division. “Our long-standing technical know-how in electric motors, combined with continued focus on innovation and established manufacturing capabilities were all key factors in allowing us to develop the best solution to grant the extraordinary performance of this unique car.”
Such results are achieved through the use of innovative technologies for the stator, rotor and overall design of the e-motors. In the stator, higher power density and efficiency are granted through a new cutting-edge solution for hairpin windings, which are made up of solid conductors, with benefits in terms of electromagnetic and thermal performance, starting from a higher filling factor (greater than 80%), compared to classic wire winding solutions. In the rotor, the optimisation in the choice of the magnets and rotor geometry allows also for the reduction of noise, vibration, and magnetic cogging, thanks to an optimised skew of the laminate stack based on the use of specific segmented magnets reducing magnet losses. In addition, an innovative technique reduces risks due to shaft current, derived from the different potential between the e-motor shaft and the chassis, which may cause a current circulation and therefore potential danger to the bearings.
Ensuring the excellent features and performances of the product is also the top-level production process, specifically designed and implemented at the Marelli’s plant in Modugno. Leveraging on the internal engineering and manufacturing capabilities, latest generation processes have been applied, starting from the rotor production, in which a cryogenic cooling process, reaching a temperature of about -200°, ensures the shaft perfectly fits into the stack. Also the stator manufacturing process is unique, due to the hairpin’s two-steps forming, one for the 2D and the second for the 3D forming. To grant product quality, an end-of-line station tests every single e-motor before it is delivered to the customer, assessing its electrical characteristics as well as its mechanical and NVH (Noise, Vibration and Harshness) performance. This adds to the over 70 quality check that are performed during the whole production process on the most important characteristics, 41 of which are fully automated.
Marelli has been developing electric motors for more than ten years. The electric powertrain product range includes both 400 and 800 Volt e-motors, featuring 3-phase permanent magnet synchronous technology, high torque density, high-performance cooling system and speeds up to 25,000rpm. Alongside electric motors, Marelli develops and produces all the key e-powertrain and thermal components needed to manage, control and optimize the complete flow of energy in electric vehicles, including inverters and power electronics, integrated e-axles systems, battery management systems and products for managing all vehicle thermal systems.