The Pandemic Is Hitting Electric Vehicle Industry Harder Than We Thought.
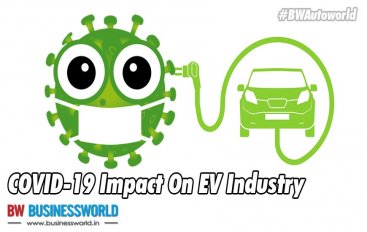
With the world coming to grips with the COVID-19 Pandemic and multiple countries going into lockdown, Automobile manufacturing is going into a shutdown globally. Since the initial contagion in China, Manufacturers have been dealing with a shortage of spare parts as Exports and Manufacturing in China was shutdown. Manufacturers can look to other sources for components. However, this will probably incur higher costs and the recertification process will take several months.
Outside of China, Italy, South Korea, United States of America and the United Kingdom are the countries most adversely affected by COVID-19, therefore, the supply of cars from most of the major manufacturers is expected to be acutely disrupted. Hyundai was the first carmaker to announce a suspension of production outside of China due to the impact of the coronavirus.
The Implications for the Electric Vehicle Manufacturers in India is particularly grim, As the battery and Component supply chains in China and East Asian countries are impacted due to lockdowns and export restrictions, The EV industry has tough times ahead.
Constrained Li-on Cell supply
As China and South Korea are adversely affected by the coronavirus, this adds a peculiar dimension for EV manufacturers. While the Lithium-ion battery packs are manufactured in-house by most manufactures but the cells are directly imported from large Chinese and Korean suppliers such as CATL, Samsung HDI and LG Chem, the manufacturers could be looking at a supply crunch and sourcing them from alternative sources is difficult. Maxson Lewis, MD of Magenta Power says “ The concept of supply shock has set in driven not only by the manufacturing close down in China but also the collapse of the supply chain globally, from the ore to the final product. The latest information we have as on date is that the cell manufacturing in China has started again but the forward logistics (shipping) is now an issue which will take another month to open out. “ This is undoubtedly an acute concern for manufacturers in India as there has been a major push towards electrification. Tarun Mehta who is the Co-founder and CEO of Ather Energy says “For a lot of OEMs the supply will be severely affected for the next few months, especially those that are dependent on international partners. Ather has a strong local supplier base for nearly 90% of the product being indigenously built and sourced but even we expect to see some delays ahead.” Recently In the Wake of the COVID-19 Pandemic, Indian Finance Minister deferred the filing of GST, this was welcomed by a lot of EV manufacturers “We want to thank the honorable finance minister for announcing the relaxation in GST returns & composition returns filing. It provides a big relief to the EV industry, which is currently facing several other challenges. – Sohinder Gill Director General, Society of Manufacturers of Electric Vehicles (SMEV)
Falling Oil Prices
Buyers may become less willing to embark on the electrification ship given the higher price point of EVs, especially as oil prices are now falling. The longer the coronavirus prevails, the more it will inevitably disrupt EV-battery supply too. “The supply shock will put out the EV plans and hence large scale investments in this space will be delayed. But this could also be the inflection point for EV from a long term perspective. Auto industries can choose to look at the traditional way of re-building their manufacturing capacities and get back to pushing the ICE engines.” adds Maxson Lewis If any short-term dips in productivity cannot be recovered quickly, companies could delay investments because of their uncertainty about the future and might ultimately lead to laying off workers. That would affect consumer confidence and expenditure, negatively affecting new-car sales but also used-car transactions and residual values.
According to report by Dun & Bradstreet - Covid19 Pandemic has spread over 163 countries some of which have direct linkages to Indian auto sector. Hence the prospects of finding suppliers in alternative markets (other than China) has turned bleak. China (27%), South Korea (19%), Germany (10%), Japan (10%), Thailand (7%), USA (7%), Singapore (4%) and Italy (2%) account for more than 80% of auto ancillary imports. All these countries are severely affected by COVID-19. A halt in production in these countries will increase the risk of supply chain disruptions for Indian automotive sector. Normally, auto companies maintain a one-month or two-month inventory, however if the supply chain remains disrupted for next two months, the Indian auto industry may face significant revenue loss.
If COVID-19 is defeated within the next two to three months, the industry could swiftly move back to normal. However, if the pandemic is not contained quickly and takes hold over a longer period, the economic impact on Electrification Journey could be severe, Industry Experts told BW