While Government Has Incentivized Local Manufacturing, Technology Integration Is Business-Critical To Accelerate Go-To-Market - Renuka Srinivasan & Shree Harsha, Dassault Systèmes
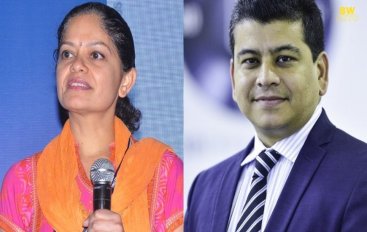
With India's commitment to net-zero carbon emissions by 2070, electric, autonomous and connected vehicles are the NEXT GEN MOBILITY SOLUTIONS. But the success of these Next-generation vehicles requires advanced creative design, shared intelligence, systems engineering, and multi-domain collaboration. Renuka Srinivasan, SIMULIA Sales Director, and Shree Harsha, Director- India Marketing and Communications & Strategic Planning, Dassault Systèmes in conversation with Siddharth Shankar from BWBusinessworld discuss how increasing the use of zero-emission vehicles and how technology frontier in India are enabling sustainability.
Excerpts
How do you see the future of sustainable mobility in India?
Mobility is one of the major contributors to the global environmental challenges; contributing close to one-quarter of the global C02 emissions1. Hence, it is natural that when we evaluate sustainability goals and net-zero carbon commitments, we have to consider sustainable mobility options. Technological innovations are building C.A.S.E (connected, automated, shared, and electric) mobility solutions, amongst which electric vehicles are gaining popularity. Smart electric vehicles can reduce carbon dioxide emissions up to 43% as compared to diesel engine vehicles2 and the Indian EV market would expand at a CAGR of 36% through 2026, while the EV battery market will develop at a CAGR of 30%3; demonstrating significant transformation and maturity of the Indian EV sector.
Taking a lead in EV development, are conscious enterprises, new-age entrepreneurs including leading OEMs, who are driven by a strong sense of purpose. Organizations helming this third age of enterprise have moved above and beyond the product and the production process empowering an equitable future for all. There is a growing environmental consciousness in the consumers, and the government is supporting the sector through encouraging schemes and budget announcements, making the future of sustainable mobility in India very promising.
With digital adoption, the third age of enterprise can further their purpose, and enjoy the following benefits
What are the technology solutions for Indian OEMs to advance self-reliance in EV ecosystem in India?
Currently, the Indian EV ecosystem is largely dependent on imports of battery packs and motors to build the vehicles, which makes up for 40-50% cost of the vehicle as well. But everyone realizes that in order to support accelerated adoption of EV fleets, India needs to be self-reliant in manufacturing electric vehicles.
While Government has incentivized local manufacturing, technology integration is business-critical to accelerate go-to-market. Digital Simulation technologies can accelerate development by integrating critical sub-systems to predict outcomes before prototypes are built. Similarly, multi-physics simulation can be leveraged to predict and verify the electric drive system performance, whilst simultaneously taking into account thermal and mechanical requirements, electromagnetic performance, durability, noise and vibration control, as well as lubrication. These technologies can enable electric vehicle battery modules and packs that exceed performance targets with a well-balanced design in thermal management, strength and durability, safety, and thermo-electrical losses.
We expect digitalization strategies to continue driving improvements in the following key areas, including:
In fact, the National Institute for Standards and Technology has launched the Digital Thread project to define and standardize methods to enable easy integration of smart manufacturing systems.
How is Dassault Systèmes bringing frontier technologies in transportation and mobility?
Dassault Systèmes’ 3DEXPERIENCE platform offers a 360-degree product development ecosystem that combines the best design and styling capabilities with user-friendly simulation and PLM4 across battery engineering, electric drive engineering, power electronics engineering, and full-vehicle engineering.
The virtual twin experience can be used to virtually create, simulate, and visualize before the physical model or system is implemented. Further, real-world data can later be used to augment the virtual twin, maintaining it in sync with the physical object allowing for better prediction of the real-world behaviour.
Our BIOVIA brand provides chemistry modeling capabilities to optimally design battery materials, CATIA provides battery libraries to efficiently use 1D simulation for cells, modules, and SIMULIA capabilities are extensively used on cell and full battery modules to improve strength, stiffness, and safety in abuse test scenarios.5
We have also launched our Electro-mobility Accelerator on the 3DEXPERIENCE platform, enabling new-age innovators and OEMs to reimagine the entire process from systems engineering to mechanical engineering virtually, 3D prototype new concepts, validate product performance, and collaborate for accelerated innovation and productive outcomes.6
Dassault Systèmes’ Industry Solution Experiences are available on both premise and on-cloud, allowing OEMs scalability, time and cost-effectiveness, and agility. We have been working with both OEMs and start-ups including Tesla, Kriesel Electric, Rimac, and Renault. One of the most exciting applications can be seen with Simple Energy, a Bangalore-based electric vehicle (EV) start-up, which announced Simple Mark 2 with a longer range of 240km on a single charge and a peak speed of 100kph, built entirely on Dassault Systèmes' development platform. They were also able to reveal the improved version within six months, expediting their go-to-market strategy.
What is the scope of virtual twin technology in expediting the start-up race in EV sector in India?
India is at the helm of an EV revolution, where OEMs are investing in R&D and factory redesign while startups and innovation labs are poised to bring new experiences to market. Hence, in this highly competitive industry, businesses that can deliver better EV models, and faster, will take a lead.
This new frontier requires reimagining the space and the integration of new technologies can be a significant engineering challenge. Here is how simulation and virtual twin technology can better connect disciplines, helping engineers review and design vehicle performance2. Further, case studies suggest that virtual twin technologies accelerate time-to-market and help bring costs down for new drivetrains, lightweight body designs, and EV batteries3, and are indispensable for the future of mobility.
OEMs can test cars for safety by employing simulation capabilities, such as running simulations to assess component durability or analyzing the thermal features of the battery for performance and safety. OEMs can develop several versions of the vehicle, or components, to select one that maximizes all criteria before mass manufacturing and do trade-off studies by generating a virtual twin of the vehicle, or components.
Primarily, there are four areas where virtual twin technology is helping EV manufacturers
What are the challenges you foresee? How can they be addressed?
One of the biggest challenges in this transformation is mindset transformation and upskilling of available talent. Cross-functional teams with electrical, electronics, mechanical, chemical, and design expertise need to collaborate. The most effective solution would be for OEMs to adopt a development platform that integrates all engineering disciplines, enables collaboration between teams through strategic insights, and adapts to the team’s requirements in real-time. The platform should enable the virtual validation of prototypes and accelerate development cycles.
Further, there is an urgent need to include and build multidisciplinary knowledge, such as in the field of mechatronics, through courses on model-based system engineering, battery modeling and simulation, motor design, and ISO standards on functional safety as part of the course curriculum. Dassault Systèmes is already collaborating with many stakeholders to implement a skill framework in universities, as well as to collaborate with businesses and academia to empower the workforce of the future. For example, Dassault Systèmes has collaborated with Tamil Nadu Industrial Development Corporation (TIDCO) to establish The Tamil Nadu Center of Advance Manufacturing (TANCAM); a first of its kind Center of Excellence (CoE) in India which will provide a dedicated IT engineering ecosystem to support students across Tamil Nadu to enable growth in EV and automotive industries among others.
Your views on the govt policies like the PLI scheme, Make in India, FAME 2, etc (In the context of the budget)
Due to various supporting schemes such as PLI, FAME, and Vehicle Scrappage Policy, the EV market in India has witnessed fast growth in the last two years. The policies have incentivized leading OEMs and new-age startups, alike, to invest and build capacities for EV production in India, while also boosting demand from customers.
We welcome Budget 2022, which accelerates India's journey to net-zero carbon commitments, and encourages the “Third Age of Enterprise” driven by purpose, especially in transportation and mobility. 2022 will be the year to deliver, and OEMs should invest in 3D technologies and simulations, to enable collaboration across the value chain and expedite go-to-market across battery engineering, electric drive engineering, and power electric engineering.
At the same time, the biggest barriers to the adoption of EVs are price considerations and charging infrastructure. As the industry progresses toward Atmanirbharta, apart from manufacturing incentives, we hope that OEMs will be encouraged to use digital platforms and virtual simulations to accelerate the development cycles and develop ready-for-market products in a resource, cost, and time-efficient manner, which will also make it affordable for customers.