Auto Industry Seeks Government Support To Boost 100% Localisation
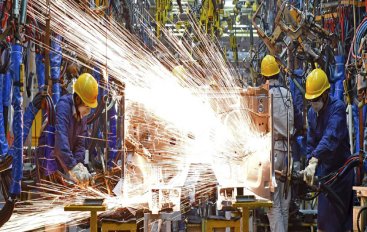
Localization refers to the practice wherein different components of the vehicles are manufactured within the country where the vehicle is meant to be sold. 100% localization within the automotive sector would be an aspirational dream in tandem with the Make in India vision of PM Modi.
The Indian Automotive Industry has gained its momentum since early January 2021 and the Indian auto components industry is expected to reach US$200 billion in revenue by 2026. The spine of the industry is the suppliers of auto components and accessories which is also an exclusive part of the auto industry. But India’s auto component manufacturing sector is yet to achieve its true potential. And this is not because of challenges in the technology but the cost of production remains the main area of concern.
While the whole nation is focusing on becoming ‘Atmanirbhar Bharat’, it is an opportunity for many sectors and contretemps for a few. The government has urged the Indian auto components manufacturers to increase localization to 100 percent and provide a push to local manufacturers to bolster the domestic supply chain and strengthen the automotive industry from its core.
Many Indian auto component industries aim to cut dependency on imports but it is easier said than done. It can be strenuous for the sector as 30 percent of the industry is still dependent on imports from other parts of the world, mainly China. While the dependency of the auto manufacturing sector on import is approximately 70 percent but some companies are supporting 75-95 percent localization. The auto sector is one of the key drivers of the Indian economy and a top contributor to the manufacturing sector. Localization will be the way forward if we want to safeguard ourselves from fluctuating exchange rates which directly impact the final model product cost.
Auto manufacturers from across the nation have sought government support for the localization of electronic components, especially semiconductors, which is currently facing a global shortage; stating it would need high investment. The factors making the differences are unavailability of resources, skilled labor availability, and technology, high cost of production, and government policies of indirect taxes such as custom and excise duties. To encourage localization cent percent, the government and auto components companies should work together on a road map for self-reliance for more localization of auto components.
Given the current scenario, most of the auto manufacturing companies have shown their interest in adopting the government’s 100 percent localization movement but seeks government support in terms of infrastructure deficit, talent crunch, industry scale-up policies, access to world-class technology and practices, remaining cost-competitive and availability of cost-effective capital. The industry is facing challenges from rapid change in technology in this segment which calls for more funds for investments in research and development. As regards the trade policy, the challenges mainly faced by Indian manufacturers are slowing down of investment in the OEM auto sector, duty on imported auto parts, and the sharp rise in imports mainly from ASEAN countries.
The Auto manufacturing industry plays one of the pivotal roles in contributing 7.1% to India’s Gross Domestic Product (GDP). The entrepreneurial community from the Auto component fraternity has wished for crucial interventions from the government on taxes, scrappage policy, import-substitution, capacity installation, and R&D.