Light Weighting For Vehicle Safety & Sustainability With Aluminium
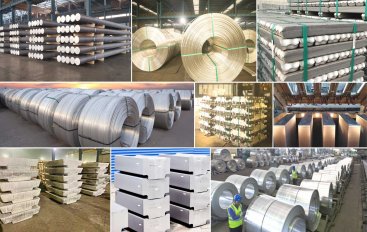
The global automotive & transportation industry is increasingly shaping up to be electrified, autonomous and environmentally sustainable. This is evidenced by the evolving consumer preferences towards electric and hybrid vehicles, and automakers increasingly using aluminium for light weighting vehicles, on account of tightening of emission norms and climate action. Aluminium is driving this change, because it offers the fastest, safest, most environmentally friendly and cost-effective way to increase performance, boost fuel economy and reduce emissions while improving safety and vehicle life.
Aluminium, The ‘Metal of the Future’ for Auto Industry
Aluminium is currently the second most used metal in vehicles and the fastest growing, a clear indication of the metal’s growing prominence in automobile manufacturing. Automakers are increasingly leveraging aluminium’s versatility to produce multiple auto components like engine radiators, wheels, bumpers, suspension parts, engine cylinder blocks, transmission bodies and body parts such as hoods, doors and even the frames. The reason being aluminium’s unique properties which lend themselves very well to the auto industry:
1. High strength-to-weight ratio: Aluminium alloys provide similar strength as that of steel while being much lighter. The average car weighs about 1300 kg. If there were no commercial limitations and as much aluminium as possible was used, it would weigh only 775 kg. This helps automakers design vehicles that are significantly lighter, faster, easier to manoeuvre, high on performance and low on carbon footprint. In electric vehicles, increase in aluminium usage in the vehicle extends its driving range by offsetting battery weight, thereby reducing cost of ownership, even with addition of more safety features.
2. Fuel efficiency: On the consumers’ side, light weighting of vehicles brings with it advantages like less fuel consumption, thereby helping with cost savings.
3. Better passenger safety: Aluminium continues to drive passenger safety as well, since pound for pound, aluminium can absorb twice the crash energy of mild steel.
4. Exceptional design flexibility: High malleable and ductile, aluminium also gives automakers exceptional design flexibility, across a wide range of automotive components & parts – from car frames to engines, battery casings, doors & windows, wheels, and many other smaller components in between.
5. Corrosion resistance: Aluminium’s natural resistance to corrosion keeps vehicles rust-free, gives them a longer life and reduces the need for frequent maintenance, thus reducing total cost of ownership.
6. Endless recyclability: Nearly 90 per cent of all the aluminium used in a vehicle can be recycled at the end of its lifecycle, thus increasing the vehicle’s salvage value.
A Catalyst for the Electric Vehicle Ecosystem
The demand for aluminium in electric vehicles (EV) and hybrids is going to be primarily driven by the need for light weighting. EVs are currently range constrained. 100 kg saved on any EV can translate to an additional 10-15 per cent increase in range. And increased range is critical to drive higher EV adoption and close the gap with internal combustion engine (ICE) vehicles. Plus, aluminium is significantly cheaper and easily available compared to alternatives like carbon fibre-reinforced composites and titanium.
According to the International Energy Agency (IEA), growth of EVs has been particularly impressive over the last three years, even as the global pandemic shrank the market for conventional cars. In 2012, about 130,000 electric cars were sold worldwide. In 2021, electric car sales touched 6.6 million, which is close to 9 per cent of the global car market. All the net growth in global car sales in 2021 came from electric cars. On an average, EVs contain 60-80 kgs more aluminium than internal combustion vehicles, so you can imagine the exponential growth in demand for aluminium in the coming years.
Beyond vehicles, aluminium will also play a critical role in building charging infrastructure for EVs, because aluminium is also used in infrastructure and electrical transmission & distribution networks. There will be more primary aluminium, extrusions and rolled products entering the EV space for light-weighting the vehicles and improving battery technologies, while also transforming the traditional models as consumers increasingly grow environmentally conscious, demanding more fuel-efficient, low-maintenance and low-GHG emitting models.
The India Scenario
The Indian automotive industry, which is gradually adopting the advantages of aluminium, is poised to become the 3rd largest automotive market in terms of volume by 2030 (as per Invest India), propelled by electric vehicles, heavy vehicles and passenger vehicles. Prior to the pandemic, India’s auto component industry imports stood at USD 15.40 Billion, which can be potentially substituted. There is immense opportunity for Indian automotive industry to leverage domestic capabilities and reduce its import dependence.
Today, globally, transportation accounts for the largest share of aluminium consumption at around 24 per cent. According to industry forecasts, aluminium consumption in transportation sector is expected to grow by 12 million tonnes from CY20 to CY30, 60 per cent of which will come from adoption of EVs. World over, there are about 3,000 applications of aluminium across various industries, whereas India has explored 300. Here lies India’s scope for expansion and value-addition.
And hence, there is a growing interest towards development of Aluminium Parks, which would see auto parts & component manufacturers set up their shops in the metal parks to procure hot metal directly from aluminium producers. Besides guaranteeing just in time delivery, it would result in significant energy savings, eliminate transmission from cross-country logistics, reduce total cost of ownership for and make the entire industry more cost competitive.
Making Mobility ‘Green’ & Sustainable
Another recent, fast-evolving phenomenon is the increasing prevalence of low carbon ‘green’ aluminium, which is aluminium that has a low carbon footprint. Major global automakers have committed to decarbonizing their operations and sourcing responsibly in order to go Net Zero Carbon within 3 decades. This will see an increase in procurement of low carbon aluminium for producing low carbon products (vehicles). The market for special aluminium alloys in the automotive segment is continually expanding with the inclusion of newer applications, as performance with sustainability becomes the metric for success in market. Clearly the future of automobiles rests on superalloys like those of aluminium making them safer, efficient and powerful.