Tyre Manufacturing Industry In India; From Fossil Fuel Vehicles To EVs
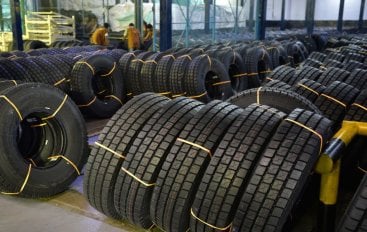
Amongst the various advancements in the automobile sector, the tyre manufacturing industry has also seen major transformations in terms of quality, versatility and efficiency, by swift adaptability to new changes and the adoption of new technologies as per the market requirements. From the cotton carcass to high-performance and durable radial tires, the technological progression has been unprecedented through the years.
With enhanced focus on product quality, production methodologies, growing exports, and acquisition of the new-age technologies, leading tyre manufacturing companies in India are not only giving healthy competition to its global peers but also strengthening the country’s overall economy.
Current Scenario
Presently, there are around 40 companies listed in the country’s tyre manufacturing sector, which is mostly organized. The industry is the largest consumer of rubber components, with natural rubber accounting for 80 percent of the total consumption and synthetic rubber for 20 percent. Raw materials account for 70 percent of the total production cost in the rubber industry.
The key factors impacting the demand and supply of high-quality rubber in India include the level of overall industry activities, cost and credit availability, transportation costs, conditions of the road network, quality and the volume requirement, vehicle loading rules and regulations, radicalization and retreading and exports.
Most tyre manufacturing companies in India these days deal in six categories of the market – original equipment manufacturers (OEMs) (significant for cars and jeeps), foreign exports, replacement market (mostly for tractors, motorcycles and mopeds), central government supplies, state transport undertakings and open retail markets.
Radialization
Radialization in the tyre industry is the transformation from the traditional tyres that uses nylon thread to radial tyres that uses steel wires. It is one of the key aspects in the Indian tyre manufacturing industry, which depicts the up-gradation of technology, the advancement and sophistication in the modern road development, new–age engineering of vehicles and the general growth of the economy.
At the present time, most cars on the Indian road run on radial tyres as it helps boost the mileage significantly and save cost on fuel up to 10 percent. Other major benefits of radial tyres include flexible sidewall, less rolling resistance, softer rides because of the layout of the tyre’s plies, stable contact with the road surface, and steel belted nature providing tougher overall construction.
However, radialization in India has been taking off at a slower than expected pace due to the unsuitability of roads for the bettered plying of radial tires, older vehicles with no suitable fitment geometry, buyers’ reluctance to pay a high price and the increasing costs of the raw materials.
Electric Vehicle (EV) Tyres
Though very much similar to the tyres used in fossil fuel vehicles, the electric vehicle (EV) tyres are slightly different when it comes to the components used for manufacturing. With less rubber and other raw materials used while manufacturing, the EV tyres are generally 20 percent lighter than their conventional counterpart. They face lesser rolling resistance, giving them a longer operational life. The design and manufacturing of the EV tyre are also made differently considering that the EVs are comparatively heavier with the batteries increasing the weight significantly.