Future Of Batteries - What Is Possible?
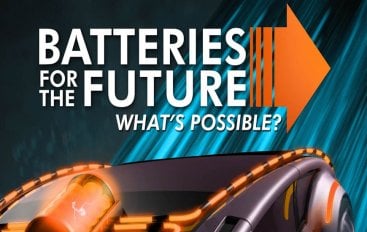
From the primitive early-stage lead zinc batteries in early-stage EV’s to the cutting-edge advanced lithium-ion cells found in most of today’s production-ready EV’s - automakers and electrochemists are yet to find the holy grail of battery cells. Ideal cells are those that can deliver the following:
Battery and its sub-componentsGiven the importance of electric vehicles to contribute towards building a sustainable planet – the internet is regularly swamped with new research on battery technologies from rechargeable lithium metal batteries to solid-state batteries and from nano-coated batteries to structural batteries, with each promising to revolutionize the electric vehicle landscape. Each of them aims to deliver the highest ever driving range with the highest factor of safety at the lowest cost. The saying goes, “Every 1% improvement in battery performance widens battery applications by 10%.
The world is moving towards reduced cobalt or cobalt-free batteries simply because its supply is concentrated, mining of cobalt uses questionable practices such as child labor and suffers from extreme price volatility. GM in the US is testing different chemistries such as nickel-cobalt-manganese-aluminum (NCMA) technology, which uses less cobalt, making the cells more stable and cheaper. Also, nickel & cobalt-free lithium iron phosphate (LFP) batteries are again seen booming—especially in China. Tesla's Model 3 Standard Range comes with LFP batteries in China. Also, CATL and BYD have moved towards a higher energy density version of LFP cells. Players such as VW and Stellanitis are following a two-pronged strategy. High nickel batteries for high-performance vehicles and nickel and cobalt-free chemistries for economy vehicles.
Mentioned below is an overview of some interesting & promising new age battery technologies:
Future of Batteries:
Lithium-Air: Lithium-air has an energy of 1300 Wh/Kg which makes it equivalent to petrol. Lithium-air batteries normally use a pure lithium anode and some form of porous carbon at the cathode. When the battery is discharged, lithium ions flow from the anode to the cathode, where they meet electrons that flow through the external circuit and react with oxygen from the air. When the battery is recharged, this process is reversed. As lithium is highly electropositive, extremely light and air is effectively massless, lithium–air batteries have the highest theoretical maximum specific energy density amongst any battery type. Designing a viable rechargeable device has proved extremely challenging. The extreme reactivity of lithium is a double-edged sword: it allows for the storage of a huge amount of energy, but releasing that energy in a controlled, safe, reversible way is difficult. Additionally, lithium-air batteries tend to die after fewer recharges and they’ve had a lower efficiency, requiring a lot more energy to charge them than can be generated by the battery later. The number of times a battery can recharge is called its cycle life, and it’s the involvement of air in the lithium-air battery that has made it difficult to get a long cycle life.
Lithium-Metal: A lithium-metal battery is considered to be the holy grail for battery chemistry because of its high capacity and energy density. This battery has a specific energy density of 300 Wh/Kg and a high cycle life of ~2000. Lithium batteries move lithium ions from the cathode to the anode during charging. When the anode is made of lithium metal, needle-like structures called dendrites form on the surface. These structures grow like roots into the electrolyte and pierce the barrier separating the anode and cathode, causing the battery to short or even catch fire. According to research by Harvard University, lithium-metal battery made of a solid-state metal material rather than lithium-ion, can eliminate the pesky dendrites and offer more structural stability than a battery consisting of liquid or graphite materials. This battery technology could increase the lifetime of electric vehicles to that of gasoline cars — 10 to 15 years — without the need to replace the battery. With its high current density, the battery could pave the way for electric vehicles that can fully charge within 10 to 20 minutes.
Solid-state Lithium: Solid-state batteries have captured manufacturers' attention with the promise of improving the safety, energy density, and range of electric vehicles. Instead of the flammable, liquid electrolytes used in conventional lithium-ion batteries, battery cell manufacturers install solid-state batteries with electrolytes in a solid form.
While it does support the rapid charge, the battery has shown poor conductivity in colder climates. Researchers at Harvard have developed a solid-state lithium-ion battery that charges up fast and charges and discharges many times without degrading much. In an EV such a battery should charge in 10 to 20 minutes and last for the lifetime of the vehicle. Alongside the potential for faster charge times without the risk of fire, the switch to solid-state batteries would not entail much change in the existing lithium-ion engineering and manufacturing processes, thus making it a viable alternative.
Lithium-sulfur: Lithium-sulfur batteries use lithium metal as the anode, an organic liquid electrolyte, and sulfur composite as the cathode, which could have a high theoretical capacity and specific energy. Moreover, Sulphur as one of the most abundant elements in the earth’s crust is non-toxic, environment friendly, which makes this battery economical and sustainable technology. This battery is not perfect. Its limited projected volumetric energy density makes it difficult to compete with Li-ion technology for applications where space is rather limited, such as electric passenger vehicles. Yet, this battery can be a suitable candidate for “light-weight” applications, such as satellites, drones, and electric planes.
Sodium-Ion: Recently CATL unveiled their first-generation sodium-ion battery. This is the first time a global battery player has announced its commercial production-ready sodium batteries. Historically speaking, research on both sodium and lithium-ion batteries started at about the same time. Over time – lithium took over and sodium couldn’t take off. But now with this announcement, sodium seems to be getting renewed interest. Good thing is that both these batteries are pretty much identical in their structure, engineering & manufacturing processes. The existing lithium-ion cell manufacturing facilities with minute alternations can be used to manufacture sodium-ion cells. The single biggest advantage of sodium ion cells over li-ion is the abundant supply of raw materials and thus, a lower cost. The raw ingredient cost of sodium is about $150 / ton viz a viz $ 5000 / ton for lithium. However, these batteries, until now, have a lower energy density than their lithium-ion counterparts. CATL first-generation sodium-ion battery is able to give about 160 wh/kg viz a 200+ wh/kg for lithium-ion batteries.
Structural batteries: This aims to be a massless energy storage system wherein the vehicle body itself aims to be an energy storage device. The need for separate batteries is reduced or potentially even eliminated. This can significantly reduce the weight of battery-powered vehicles or other objects by incorporating batteries into the structure of the object. This could result in significant efficiency gains. A lighter electric vehicle, for example, will require less energy to drive if all other things are equal. Research in this area is happening since 2007, however, the latest prototype from Sweden exceeds the energy storage, stiffness, and strength of all its previous models – thus giving actual hopes of commercialization. This breakthrough has been delivered using carbon fibers as the battery's negative electrode
Silicon-based anodes: Among the new chemistries & materials being studied, silicon is demonstrating good potential as an anode material to replace or to be added alongside the commonly used graphite. Silicon has been shown to have a high theoretical gravimetric capacity, approximately 10X of graphite, however, however, silicon-based anodes have traditionally been suffering from rapid degradation with each cycle. A few battery material players in the US claim to have taken care of this problem however, they haven’t commented on the cost aspect yet.
This list given above is only indicative. The scale of investments, funding, and govt grants going into the R&D for batteries today is beyond imagination and electrochemists worldwide are consistently doing their research to come up with new chemistries.
Our Views
Any of these batteries shouldn’t be ruled out. All these new chemistries mentioned above promise a glorious future for electric vehicles and for all other applications which rely on batteries. While success in the laboratories is a critical first step, there is a long way and a lot of uncertainty from lab-based success to success in series production. We believe that only those handful of new technologies will become big which are compatible with existing lithium-ion manufacturing facilities and processes or those which will need very minor retooling and retrofitting in the existing li-ion factories for scale-up. The massive scale of investments already made in lithium-ion factories globally is kind of irreversible. No one company can do it all. Players will need to constantly invest in and partner with new-age technology companies to stay up to date.
EV world right now, at least for performance vehicles is dominated by Nickel & cobalt based chemistries. Nickel content will continue to increase in this segment. NMC 111, transitioned to 622 and now we are already seeing 811 (with eight parts being nickel). Further, for the economy vehicle and stationary application segments, we will see nickel-free & cobalt-free chemistries ruling the market. We are already seeing US-based players such as C4V & IM3NY developing such batteries which have all the benefits of LFP batteries including lower cost, higher safety & higher cycle life. Over & above this, their proprietary chemistry BM-LMP offers an energy density of 20% higher than the LFP batteries and is already being manufactured at scale in the US using the existing li-ion manufacturing plant & equipment.
Research on alternate batteries mentioned above will continue, however, we are not expecting to see any commercial success before the next 5–7 years. We believe Lithium-Ion will still be the dominant battery and versions of lithium batteries will keep on emerging. In the li-ion space, the cathode will continue to have reduced or eliminated cobalt and the anode will start getting more silicon instead of graphite.