India’s Tryst With EVs: A Tough Road Ahead
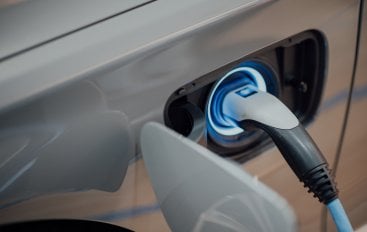
In the auto industry, the adoption of electric vehicles (EVs) is at an inflexion point across the globe. Several factors have impacted this trend, especially the growing awareness about the pitfalls of dependence on fossil fuels and the impact of climate change. The Indian Government has also taken a bullish stance on achieving carbon neutrality through the rigorous and fast-paced implementation of EVs. Prime Minister of India, Narendra Modi, has pledged to make India carbon-neutral or Net Zero by 2070.
On the policy front, the Government of India is working tirelessly to facilitate the country’s transition to EVs through policy-led supply and demand-side incentives. One of the prominent ones is the Faster Adoption and Manufacturing of Hybrid and Electric Vehicles in India (FAME) scheme with an allocation of $96.8 million. Under FAME I and FAME II, the Government offers subsidies for two- and three-wheelers, hybrids, e-cars, and e-buses, as well as to establish EV charging infrastructure. Apart from the central government, many state governments in the country have set ambitious EV targets and are leading the transition towards EVs by signing multiple MoUs with industry players.
Over the next five years, the electric vehicle (EV) segment in India is expected to attract investments of over $12 billion, or close to Rs. 1,00,000 crore, across the automotive value chain. Both established and new players are scrambling to set up EV or EV component manufacturing facilities.
This trend is not just limited to India. In the US too, President Joe Biden recently passed an executive order to end the sale of petrol vehicles by 2035.
Battery Quality could prove to be the Achilles Heel for EVs
Despite the stated intent and policy initiatives, the large-scale transition to EVs is fraught with challenges around range anxiety and the lack of drivable roads and charging infrastructure. The battery lies is at the heart of EV vehicles. Yet, staggering competition in the space has led to a deluge of cheap quality batteries, resulting in fatal accidents, especially in India. Recently, several instances of electric two-wheelers catching fire have dominated headlines. Lithium-ion batteries are especially prone to catching fire if they are damaged or unsuitably manufactured or have software issues.
Challenges around Battery Swapping
Range anxiety is another concern. To address this, the Indian Government announced a new policy to encourage battery swapping, a service that allows EV owners to swap discharged battery blocks with freshly charged ones at swap stations. This is faster than charging the vehicle and reduces range anxiety for drivers.
However, sustaining a robust battery swapping infrastructure requires standardization of EV batteries, which may hinder domestic innovations in battery technology. Also, efforts to align battery swapping standards with global guidelines could lead to greater reliance on imported technologies, defeating the very purpose of the ‘Atmanirbhar Bharat’ mission. Interoperability standardization of batteries proposed in the Union Budget could therefore lead to import dependency, customer frustration, increased costs, and the creation of artificial monopolies, thereby discouraging open markets.
Ensuring Safe and Reliable Batteries
To ensure battery safety, measures such as stringent validation of both virtual and physical design and adherence to manufacturing standards are much needed. In addition, some of the aspects that need to be considered include the choice of battery (LFP, NMC) considering the functional environment and drive cycle and battery cooling/thermal management to address thermal runaway.
Validation and quality assessment at the cell level as well as battery level is needed to address issues such as battery fires. Here, the Government has an important role to play in setting up stringent safety standards such as AIS 156 and building policies to encourage R&D in cells and the complete battery system.
Also, there needs to be due consideration to safety parameters throughout the design and optimization stages. These include impact protection and thermal management; production including electronics enclosures and CNC manufacturing, and quality inspection, which includes industrial CT scanning and non-contact contour measurement. Battery Management System must be designed to address battery over-charging and over-discharging, battery health, safety and thermal management.