Scientists Invented Improved, Low-Cost Magnets For EVs, Can Reduce Costs Of EVs
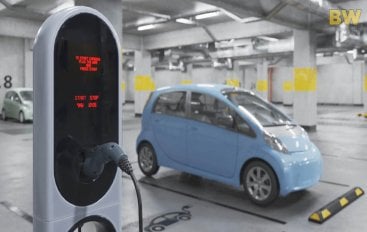
Researchers have invented enhanced, low-cost, heavy, rare-earth-free high Nd-Fe-B magnets, which are highly demanded after electric vehicles and could lower their price.
Brushless DC (BLDC) motors made of rare earth Neodymium Iron Boron (Nd-Fe-B) magnets are used in more than 90 per cent of electric vehicles. The Nd-Fe-B magnet has been one of the most demanded permanent magnetic materials for many applications since Sagawa discovered it in 1984. This is because of its exceptional combination of magnetic properties.
Nd-Fe-B magnets used in electric vehicles (EVs) have a high resistance to demagnetisation because they operate at high temperatures between 150 and 200C. Pure Nd-Fe-B magnets lack this ability. As a result, an alloy containing dysprosium (Dy) metal is added to increase demagnetization resistance. Researchers from all over the world are working to improve Nd-Fe-B magnets' coercivity (resistance to demagnetisation) without using expensive Dy. The scientific community has chosen to enrich the space between the Nd-Fe-B magnet's grains with "non-magnetic" materials using the appropriate heat treatments in order to increase coercivity (grain boundary diffusion).
The coercivity of Niobium (Nb)-containing Nd-Fe-B melt-spun ribbon has recently been improved by the grain boundary diffusion process (GBDP), according to researchers from the Centre for Automotive Energy Materials at the International Advanced Research Centre for Powder Metallurgy & New Materials (ARCI), an autonomous Research and Development Center of the Department of Science and Technology (DST), Government of India. The precipitation of Nb, which enables the enrichment of Copper (Cu) at the grain borders and limits grain development during grain boundary diffusion, has been reported to strengthen the resistance of Nd-Fe-B powders to demagnetization. This study was reported in with the coercivity value of 1 T at 150 C, which is crucial for automotive applications.
In accordance with the Atmanirbhar Bharat mission of the Government of India, ARCI has taken the risk of setting up a pilot plant for the production of near net-shaped Nd-Fe-B magnets through a significant project funded by the Science and Engineering Research Board (SERB). The aforementioned strategy will be investigated for the magnets produced in the pilot plant.
The novel approach might potentially be utilised to commercially produce Nd-Fe-B magnets in India, decreasing the need for imports to provide the primary needs of the car industry.